Revolutionizing Freight and Transport Through Digitalization
The modern-day supply chain, a critical component of global commerce, faces increasing challenges, including those presented by long-term contract challenges. With ‘Supply Chain Air Freight Long-Term Contract Challenges’ at the forefront, the intricate nature of contracts, numerous stakeholders, and the rapidly changing landscape of cargo movement become even more evident. There’s a need to streamline processes and improve efficiency. The pandemic has only amplified these issues, but where there’s a challenge, there’s also an opportunity: the potential for digital transformation in freight and transportation.
The Problem Deep Dive
Air Freight Contract Duration
Prior to the pandemic, air freight contracts within the supply chain usually lasted a quarter or a year. Yet, the crisis drove numerous freight forwarding firms and direct customers to secure longer-term agreements to ensure they had adequate space. However, a notable downside of these extended contracts is their strict penalty clauses for early termination. While these penalties offer security to service providers against abrupt cancellations, they pose constraints for clients, limiting their flexibility. Today, there’s a prevalent trend of multi-year charter contracts still being active in the market.
Complex Paperwork and Compliance
With global trade comes the need for rigorous documentation. Freight contracts, regulatory compliance paperwork, customs declarations, and more are now an inevitable part of the supply chain. Longer-term contracts further complicate this scenario. This often translates to tedious manual processes, delays, and potential for error. Administrative inefficiencies, particularly with customs paperwork, can hold up cargo for days, considerably influencing cost and delivery timelines.
While border compliance procedures have long been a challenge, with almost 30% of all global trade costs in 2020 attributed to them, it’s worth noting that such issues aren’t directly tied to the pandemic. Instead, geopolitical events such as Brexit play a significant role in shaping these documentation procedures.
Fragmentation in the Supply Chain
One of the most pressing challenges is fragmentation and lack of visibility across the supply chain. From manufacturers to transport providers to end retailers, the absence of a unified platform creates inefficiencies and uncertainties. A shipment in international trade often involves 20-30 parties and over 40 documents. Such fragmentation can elevate costs by 15% and slash service quality by 30%.
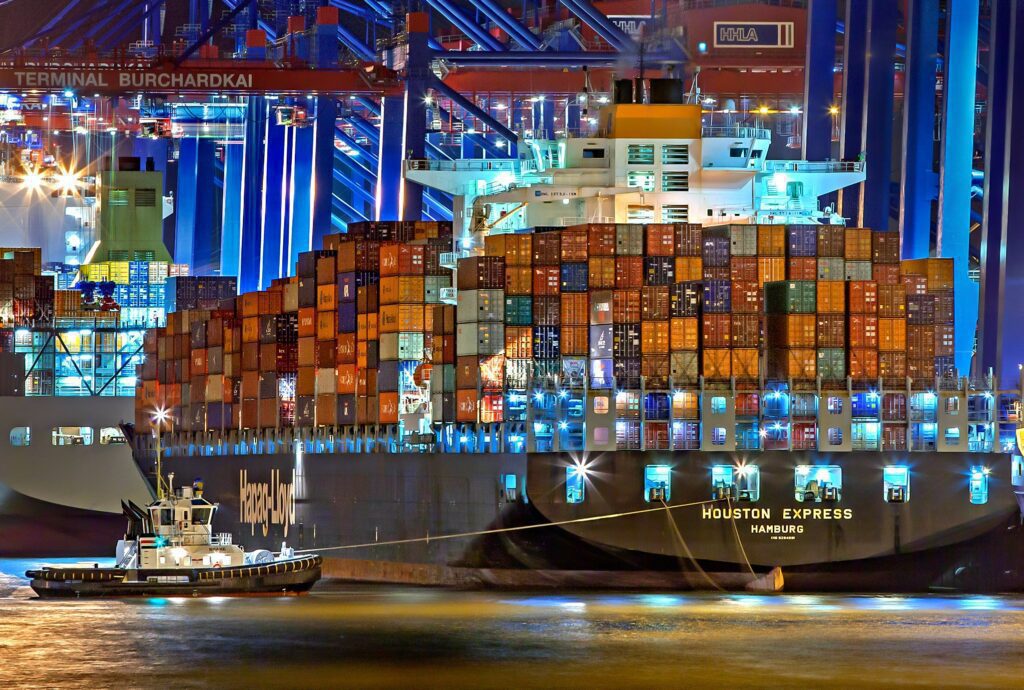
Pandemic's Impact
COVID-19 further complicated the logistics landscape. The unpredictability brought about by the pandemic made stakeholders seek guaranteed access to transportation space and rigorous compliance adherence. This desire for stability, however, collided with a fluctuating contract landscape and volatile cargo movements, leading to a magnified demand-supply gap.
In April 2023, the International Air Transport Association (IATA) highlighted a pressing issue of overcapacity in the global air cargo sector. While the demand for air cargo decreased by 6.6% compared to April 2022, the available capacity to transport cargo surged by 13.4%, exceeding pre-COVID levels. This disparity between reduced demand and increased capacity presents a significant challenge for the industry.
Embracing the Digital Era: The Path Forward in Global Trade
Integrated Digital Platforms
To address the complex landscape, integrated digital platforms have emerged as a potent solution. These platforms offer centralized contract management, automated compliance checks, and real-time visibility into cargo movements. Firms with digital supply chain platforms can boost their operational efficiency by 10%. A staggering 85% of enterprises predict that within the next half-decade, integrated platforms will become pivotal in supply chain management. Integrated technology isn’t just a buzzword.
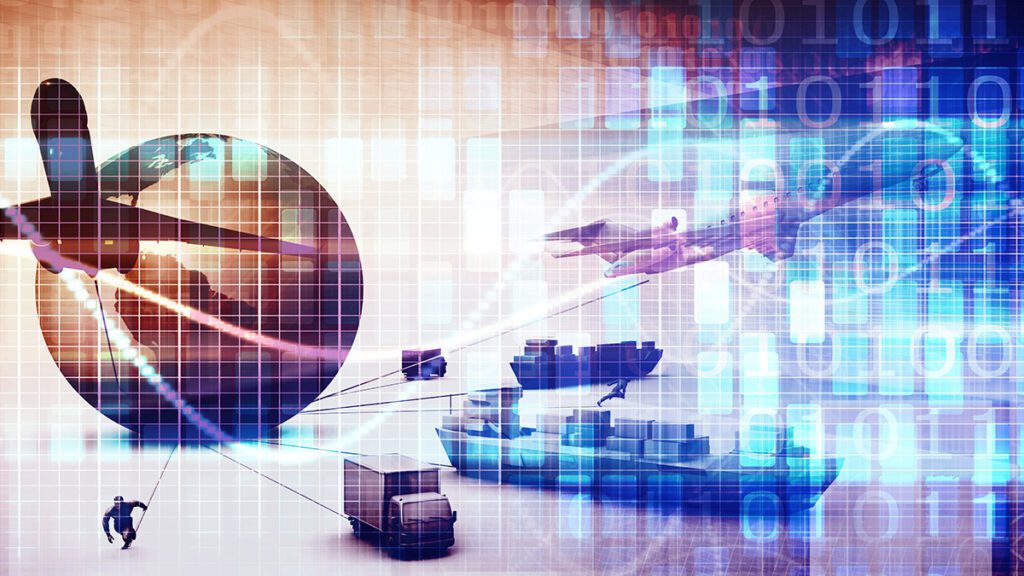
A comprehensive look at the ‘Digitally-Driven Growth: A Holistic Approach to Aligning Supply Chain Objectives with Broader Business Goals‘ case study reveals its tangible benefits. The study found that such technology can facilitate seamless communication and data-driven operations in the supply chain.
Blockchain & Smart Contracts
The integration of blockchain ensures data security, transparency, and verifiability. Smart contracts can automate contract execution based on predefined conditions, significantly reducing manual intervention and the potential for disputes.
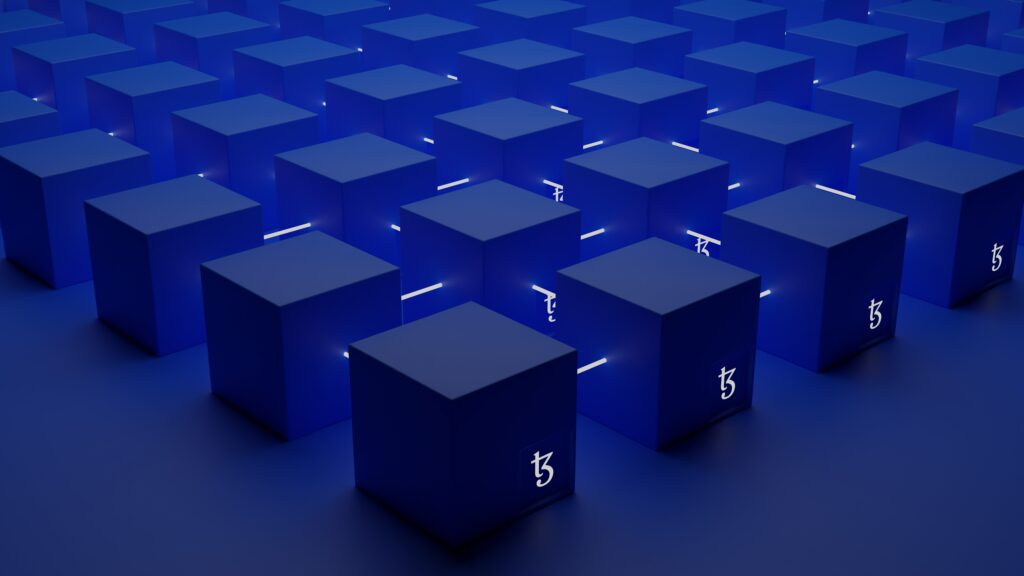
A recent research publication from Agile Dynamics estimates that blockchain technology will increase the Global GDP by $2.1 Trillion and almost half of it will come from B2B growth markets, which indicates the expectation of widespread adoption and innovation of blockchain in various industries and markets globally. The adoption of smart contracts can cut business expenses by an average of 13% by eradicating manual touchpoints and middlemen.
Predictive Analytics
Advanced analytics provides stakeholders with predictive insights into market trends, allowing them to anticipate challenges and adapt accordingly. It also aids in the optimization of routes, storage, and even pricing.
According to Harvard Business Review “Retailers lag in adopting advanced data analytics due to cultural resistance, organizational issues, talent shortages, unclear processes, outdated systems, and data management challenges. It recommends fostering an analytics-friendly culture, organizational redesign, and strategic investments in technology and talent for businesses to leverage the full benefits of analytics.”
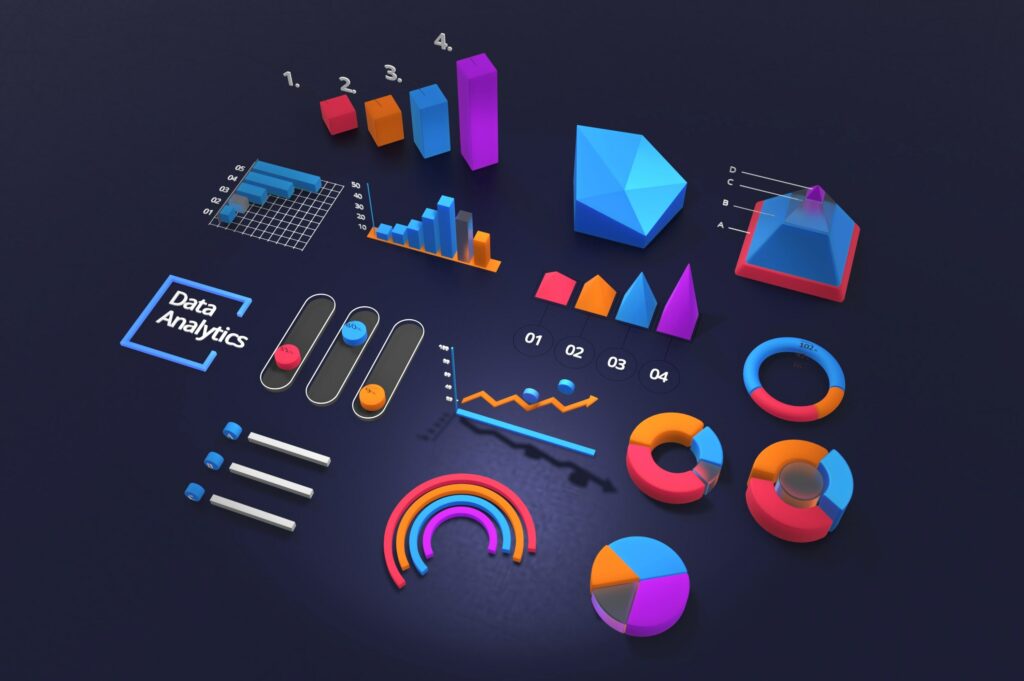
Firms employing advanced analytics boast 33% higher profit margins compared to their non-adopting counterparts. 62% of retailers and manufacturers saw significant enhancements in their supply chain operations after incorporating predictive analytics.
Analytics not only helps in anticipating market trends but also in evaluating contract performance. By applying analytics to contract terms, businesses can assess metrics like revenue productivity per container or per mile. This offers insights into whether long-term contracts are financially viable or if they need revisiting.
Analytics-Driven Contract Management
In the realm of digitalization, merely moving contracts to digital platforms isn’t enough. The true power of digitization lies in leveraging analytics to understand and optimize contract terms. For instance, determining the ‘revenue productivity per container’ or ‘revenue productivity per mile’ can offer insights into the true cost and effectiveness of long-term contracts. Such granular analytics can guide companies on whether the long-term contract model is beneficial or if adjustments are needed. By evaluating these metrics, organizations can make informed decisions about restructuring their contracts, ensuring they get the best return on investment.
End-to-End Visibility
One of the most invaluable features of these digital platforms is the promise of end-to-end visibility. For companies, this means being able to monitor their supply chain in real-time, right from the point of origin to the final delivery, ensuring better coordination and decision-making.
According to this article form Supply chain digital, “Supply chains are lagging in adopting modern visibility technology, with a lack of real-time data and cross-company collaboration hindering progress, says Ryan Closser from FourKites. A Deloitte report reveals only 13% of firms can map their entire supply chain, while 22% lack visibility beyond immediate suppliers. “
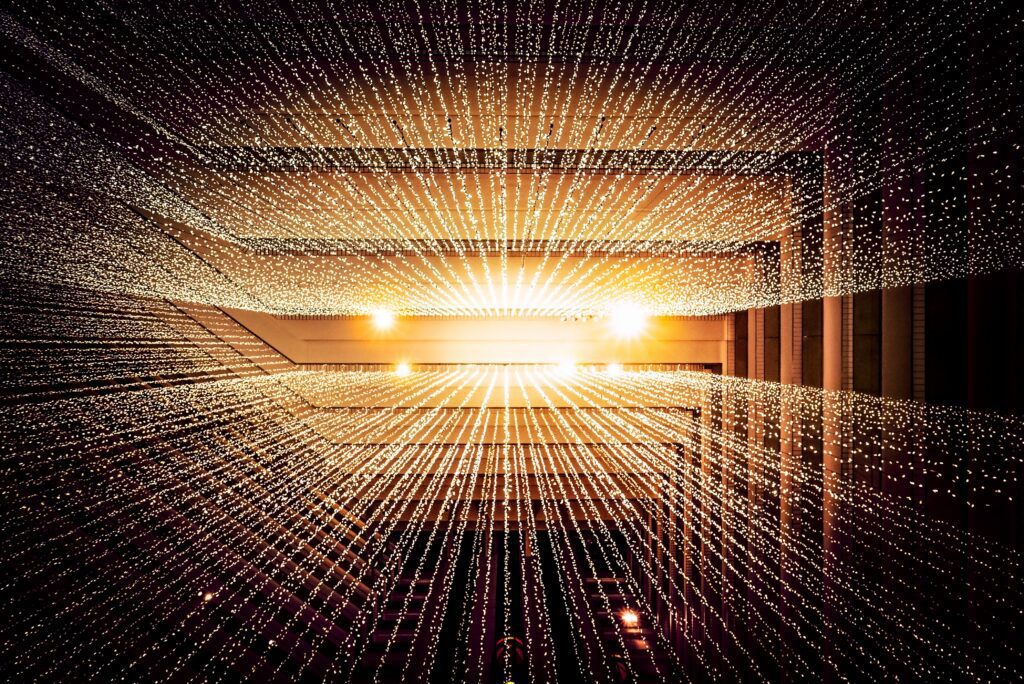
Visibility is vital for operational efficiency and future resilience. Businesses with end-to-end supply chain visibility enjoy a 20% reduction in the cost of goods sold. This is evident in the case study of ‘Digital Transformation in Logistics: Enhancing Efficiency and Performance with End-to-End Supply Chain Visibility.’ In this study, it was clear that digital tools can significantly enhance efficiency, enabling real-time tracking and data-driven decision-making in optimizing the supply chain. It underscores the necessity of such visibility tools in today’s complex logistics landscape. Enterprises that possess real-time supply chain transparency can diminish stock-outs by 50%.
The digital tide waits for none
The freight and transportation sectors are at the forefront of a pivotal digital transformation. As the pandemic amplifies global challenges, the industry’s course is indelibly linked to its prowess in embracing and leading with digital innovations. Beyond just strategic moves, digitalization emerges as an essential pillar for resilience, growth, and efficiency in our complex global commerce matrix. This isn’t about passive adaptation—it’s a clarion call.
The data sends a clear message: Embrace digital tools to eradicate inefficiencies and cultivate nimble, adaptable supply chains. Integrated platforms, blockchain, predictive analytics, and end-to-end visibility aren’t just advantages; they’re imperatives. Every stakeholder, from manufacturers to retailers, must spearhead this change.